Technical Manager
Job
Overview
- Oil, Gas and Chemical, Power and Renewable Energy, Industrial, Manufacturing, Rail, Infrastructure and Construction, Craft
- Permanent
This vacancy has now expired. Please see similar roles below...
Company is seeking a Technical Manager to join our team. The Technical Manager is responsible for managing the day-to-day responsibilities of the Chemical side of the Auriga Polymers Spartanburg Plant. The Technical Manager works very closely with the with other departments and plant operations.
Responsibilities:
• Provide the right resources to maintain a safe workplace, fulfill all legal requirements, manufacture products according to customer requirements, reduce cost, improve equipment reliability, keep a good work climate, and promote continual improvement.
• Ensure employees know their job risk and have the knowledge, skills, and tools to take mitigation actions to control these risks.
• Define expectations and success measures to improve the profitability of each product line and ensure they are communicated and understood throughout the organization.
• Ensure we have the right people (Skilled, Talented and Motivated) to accomplish all defined goals.
• Understand the business strategy for the unit and identify technology-driven opportunities for improvement.
• Assist Area Managers in prioritizing technology improvement opportunities.
• Support the Area Managers in development of the site capital and process improvement plans.
• Participate in efforts to reduce energy usage in the BP area.
• Provide primary plant technical support for the Polymer BU.
• Provide technical support to Spartanburg BP operation.
• Work with tollers to establish processes for new products requiring crystallization, SSP and/or compounding as needed.
• Ensure the Quality System Process is effectively monitored to demonstrate the process is achieving planned results and is conforming to ISO requirements.
• Ensure Laboratory excels in behavior-based safety program (SOAR), achieves proactive safety goals (JHAs, action plans, etc), and flawlessly executes the SWP.
• Monitor the site’s Manufacturing System to ensure compliance with the ISO 9001:2015
Expectations
• Set the expectation that all incidents are preventable. Strive to create a culture that embraces behavioral based safety and support further education of key safety risks and accountability is clearly understood. Expectation is zero injuries and zero NOV's.
• Conduct periodic audits (safe assessment) of activities involving the safe work permit process and ensure flawless execution-
• Create an atmosphere that motivates employees to identify and challenge potential non-compliant behavior and report it to appropriate company resources in a timely manner.
• Execute capital projects (Compliant, Safe, right, on time and on budget) that help improve the business performance and fulfill compliance and business objectives.
• Customer Satisfaction – Provide product that meets or exceeds customer requirements.
• Improve TQA past due performance.
• Encourage potential problem analysis mentality before changes are executed to ensure success.
• Budget Control – ensure that all areas manage budgets effectively and spending is controlled not to exceed the total budget for each cost center.
• Facilitate trials for production of standard.
• Monitor the site’s Manufacturing System to ensure compliance with the ISO 9001:2015 standard.
• Ensure adequate resources are applied to maintain an efficient and effective Quality Management System
• Integrate quality roles into the core work processes
• Continuously improve the quality system to meet or exceed the customer requirements
• Provide support to meet Q3 and waste reduction goals in BP.
• Help identify and implement energy reduction activities in BP.
• Support certification to Food Safety Standards in Batch.
• Know the Quality System Process (QSP).
• Know the ISO requirements for the QSP.
• Define gaps and recommend improvements.
• Implement improvements.
• Provide performance data.
• Provide coordination and assistance for audits.
Requirements:
• 10 years or more manufacturing experience
• Management or Team lead experience
• Degree in Chemistry or Chemical Engineering preferred
• Excellent time management and communications skills
To be considered for employment in this position you must be eligible to work in the United States without company sponsorship now or in the future.
We are an equal opportunity employer.
Drug tests are required unless prohibited by state law.
This employer uses E-Verify.
Job Type: Full-time
Pay: $120,000.00 - $140,000.00 per year
Benefits:
• 401(k)
• 401(k) matching
• Dental insurance
• Employee assistance program
• Flexible spending account
• Health insurance
• Health savings account
• Life insurance
• Paid time off
• Professional development assistance
• Relocation assistance
• Tuition reimbursement
• Vision insurance
Schedule:
• 8 hour shift
Supplemental pay types:
• Bonus pay
We are an equal opportunity employer. All qualified individuals will receive consideration for employment without regard to race; color; age; sex; sexual orientation; gender identity; religion; national origin; disability; veteran status; genetic information; or any other criteria protected by governing law.
Sign-up for Job Alerts
Our latest jobs
Negotiable
United States, Spring, Texas
Negotiable
United States, Houston, Texas
$ 90000 - $ 95000
United States, Mooresboro, North Carolina
Our insights
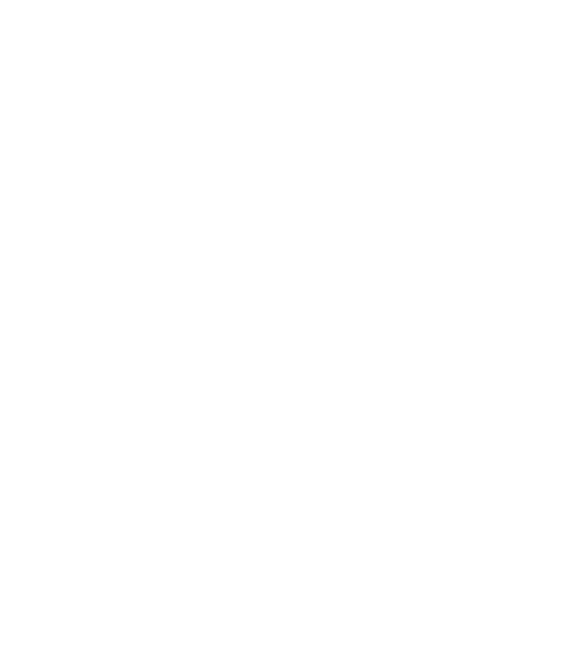
Looking for a new role?